Ja,ha haa....
Alvast even de gegevens er bij zetten,voor later zeg maar.......
Voor het vergrote Spitfire deel kan ik in het najaar wel ''ribben en rompformers'' intekenen.
Tja,en hoe dik de huid wordt?
Dat wordt flink testen met PLA,ABS,PETG etc,etc.
Ook zal ik mij,net zoals Koos,goed moet verdiepen in de nog aan te schaffen software.
(Prusa i3 mk2)
Gisteren vertelde een persoon bij het Fab lab waartoe de huidige voor mij onbetaalbare bedrijfsmatige software toe in staat is om berekeningen uit te voeren.
Ik vond het heel mooi om te zien met welke oplossing die software kwam.
Ik weet zeker dat de volgende generaties hier op het modelbouwforum met hele mooie werkstukjes komen.
Groet:Robin
Alvast even de gegevens er bij zetten,voor later zeg maar.......
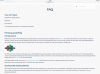
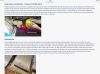
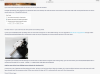
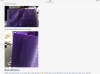
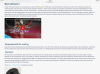
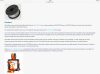
Voor het vergrote Spitfire deel kan ik in het najaar wel ''ribben en rompformers'' intekenen.
Tja,en hoe dik de huid wordt?
Dat wordt flink testen met PLA,ABS,PETG etc,etc.
Ook zal ik mij,net zoals Koos,goed moet verdiepen in de nog aan te schaffen software.
(Prusa i3 mk2)
Gisteren vertelde een persoon bij het Fab lab waartoe de huidige voor mij onbetaalbare bedrijfsmatige software toe in staat is om berekeningen uit te voeren.
Ik vond het heel mooi om te zien met welke oplossing die software kwam.
Ik weet zeker dat de volgende generaties hier op het modelbouwforum met hele mooie werkstukjes komen.
Groet:Robin